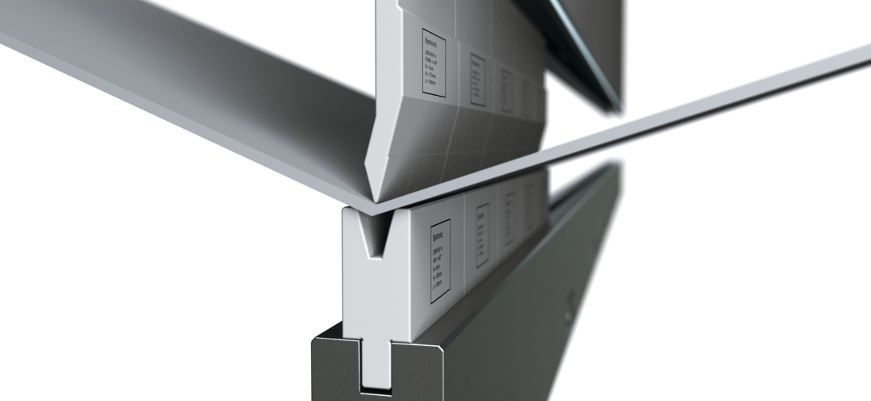
Sheet Bending Principles
Sheet bending is a process of metalworking without removing the saw, whereby the inner part of the transverse section is shortened and pressurized, while the outer part is prolonged and under tensile stress.
Sheet bending can be divided into:
- Circular sheet bending
- Angular sheet bending
- Profile sheet bending
Generally, sheet bending is the most commonly used sheet and metal processing procedure by a plastic deformation. Sheets and metals are most often cold, and if they are thicker, they must be heated.
The bending sheet, during the bending process, is under the influence of plastic and elastic strain, which results in:
- The material absorbing the desired shape
- The material expanding due to the cessation of the elastic stress
Because of the elasticity, the sheet, or the metal, has to be subjected to greater bending, in order to obtain the desired angle.
Circular sheet bending
Circular sheet and metal bending is carried out using a 3-roller bender, ie. 4 roller bender. The first and the second roller serve as the support to which the sheet is leaning, while the third roller, unlike the first two, is larger and hasn’t got its own drive. The large, that is, the first roller can move and thus controls the bending. Most circular bending machines have parallel rollers, but there are also machines where the rollers are horizontally spaced, which allows the cylindrical bending.
The four roller sheet and metal bending machines, provide different bending modes. Three rollers serve only as a support, while one roller is working. The rollers that serve as a support can move or change their position. The mode of operation alone, with the four roller bender, is almost identical to the three roller bender mode.
The advanced technology has enabled the development of numerically controlled metal and sheet bending machines, making them more precise and better at bending.
Angular sheet bending
Angular sheet bending is used to bend long and thin sheets. The machine used in this operation consists of two fundamental parts. This bending mode uses a bending force of 25 tons.
The following presses can be used for angular sheet bending:
- Manual mechanical bending presses – the machine consists of a work table where a sheet or a metal that needs to be bent is put. In this way, sheets up to 2 mm thick can be bent
- Mechanical bender – such a bender consists of a desk with a matrix mounted on it. The drive of such a bender is an electric motor (three-phase electric motor). The sheet, that is, the metal that is being bent, is placed manually on the work desk. Once all the parameters are set, the bending parameter control is automatic.
- Hydraulic benders – If bending requirements cannot be met by the above-mentioned benders, the hydraulic bending is needed. This bender uses considerably larger bending pressures, which allows it to bend thicker and harder materials.
Profile sheet bending
By profile sheet bending, products of relatively large lengths are obtained. In this bending process, we are usually talking about the polygonal bending. Profile metal and sheet bending, leads the sheet, ie, the metal through a series of rollers where each roller performs a gradual bending. Machines that perform profile bending, can bend up to 200 meters of metal ie, sheet per minute.
Metal and sheet bending is a process of cold (hot in some cases) metal processing, during which, the benders that weigh up to several tons are used.